Below are some of the principal areas that need to be understood by everyone taking part in the event.
- An understanding of the Fire & Emergency Procedures of the venue and the protocol for First Aid assistance. All incidents to be reported to the Organizers or the Health and Safety Officer, including near miss accidents.
- The emergency gangways, as indicated on the Site Locations Plan, must be kept clear of obstructions, at all times, throughout build-up, open days, and breakdown.
- All work areas must be maintained free from general waste materials that could be a hazard to anyone working on the stand. This also allows for any potential hazards to be clearly visible.
- Hard hats should be worn when working beneath or near overhead working, or if this is not practical, access to such areas should be restricted.
- PPE including Steel Toe Capped Footwear must be worn during the Construction phase of Build Up and Breakdown. When in external loading bays Hi Visibility Jackets must be worn.
- Other suitable PPE relevant to the job being undertaken must be worn e.g., hard hats, goggles ear defenders etc. NB: PPE is the last line of defence when all other alternatives have been considered. PPE must be suitable and sufficient for the job and employees trained in its uses and limitations.
- The Health and Safety Representative for either the contractor or the exhibitor (depending on the user) is responsible for ensuring the safe use and storage of flammable liquids and substances, and segregation from waste and other risk areas. Compliance with the COSHH regulations is required.
- Portable power equipment must only be operated by fully trained and certified personnel for the purpose for which it was designed, safety guards must be correctly fitted and used.
- Portable electrical tools must be used with the minimum length of trailing leads and must not be left unattended with a live power supply to it. Trailing leads and electrical cables must not cross over gangways, doorways or fire exits. Any work using power or hand tools must be restricted to the stand space, i.e., no drilling or sawing in the gangways.
- All materials used for construction or displays must be to Local Authority Standards and not less than British Class 1 standards of flammability (see Materials for Stand Construction on pg. 116)
- A hot working permit must be obtained prior to commencement of hot work (ox-acetylene, cutting/welding, arc welding, gas/oil blowlamps, grinders, tar boilers, soldering).
- Safe working at height is a priority whether using ladders or scaffold towers. For more information see Working at Height (on pg. 25) and visit www.stop-the-drop.co.uk.
- All staff working on site (whether from our own company or those of any company contracted by you) are aware and adhere to the current Working Time Regulations (S.I 1998/1883). Guidance regarding these regulations can be obtained by contacting your local HSE (Health & Safety Executive) office or visit https://www.hse.gov.uk/contact/faqs/workingtimedirective.htm
- All construction materials, ladders, trolleys etc. must be removed from the building prior to any public entering the building. Similarly, no contractors will be permitted access for breakdown until all members of the public have vacated the building.
Any queries with regards to the above please contact ops.fit@montgomerygroup.com
On-site any violations or concerns regarding the above points should be reported to the Hall Floor Manager or to the Organiser’s Office. Internal telephones are located around the hall perimeter to contact Fire Emergency Services Dial 3333 or dial +44 (0)121 767 3333 from an external line. To contact Medial Emergency Services Dial 2222 or dial +44 (0)121 767 2222 from an external line. To contact Security Emergency Services Dial 6666 or dial +44 (0)121 767 6666 from an external line.
Special Conditions for the Display of Machinery
PLEASE NOTE – The delivery of all large machinery will be scheduled in during build up. The schedule will be managed by our lifting contractor ILS and the NEC traffic department. Please contact ILS as soon as possible if you require the use of a forklift or crane at the exhibition PLEASE CONTACT:
Michal Blok
Tel: +44 (0)247 633 7955
Email:Michal@i-l-s.co.uk
Exhibitors lorries with HIABS on the trailer will only be allowed in the hall if the organisers and ILS have been notified. Operators will be asked onsite to show certificates.
If you need to use any specialised glass handling equipment, please send full details of the intended equipment to the organisers and ILS. Operators will be asked onsite to show certificates. Please ensure this is included in your risk assessment.
IMPORTANT NOTICE ON HIABS: - If you will be using a HIAB at all you are required to get in touch with the organisers asap.
- All new machines promoted at the exhibition shall be assumed to be offered for sale within the EU. As such, all machines need to display a CE mark. Failure to display a CE mark requires the exhibitor to place a clear notice on the machine that it may not be sold within the EU and the organisers reserve the right to request the removal of the machine.
- Every machine is to be guarded in compliance with the requirements of the European Machinery Directive (89/392 as amended by 91/368/EEC) implemented in the UK by the Supply of Machinery (Safety) Regulations 1992. All such guards shall be considered normal for the operation of the machine in an industrial setting. Where guards are removed or made of special material for display purposes this should be indicated on the machine.
- Stand plans are to show the location, size, in-feed and out-feed arrangements of all machines that are to be operational at any time during the exhibition. Stand Plans along with the Construction Phase plan consisting of Risk Assessments, Method Statement, Welfare Form and Better Stands Table are to be sent to Johanna via this link no later than FRIDAY 14 FEBRUARY 2025. Should you have any questions or queries please do contact Johanna Shirley directly.
- All machines intended for demonstration need to be connected to a suitable operational waste extraction system, full details of which need to be submitted to the organisers contact Sophie Wood. Failure to comply with this may result in the prohibition of such demonstrations.
- Exhibitors have a duty to ensure that machines and equipment are used only for the purpose for which they were designed.
- Where machines are not sufficiently stable as freestanding model’s exhibits are to be secured to the floor or other structure.For information on fixing to the hall floor please contact eventorders.nec@necgroup.co.uk.
- No machines shall be operated unless the required guards and safety devices are in position, properly and correctly adjusted and in full working order. A protective safety cover should be placed over the teeth of band saw blades in automatic band saw sharpening machines. When demonstrating such machines Exhibitors need to ensure that visitors are prevented from coming into contact with exposed band saw teeth.
- Machines with exposed moving parts or cutters are to be protected by a suitable barrier around the parts or demonstration area.
- Safety barriers shall be not less than 1.5m from the nearest danger point and of a height to prevent people reaching in. The Organiser may, at their absolute discretion, insist that a safety barrier is erected around any demonstration area or exhibit at the cost of the exhibitor.
- Where machinery is being demonstrated adjacent to an aisle the Organiser may require that a fixed barrier one metre high shall be erected along the front of the exhibition stand at the cost of the exhibitor.
- Suitable emergencies stop controls are required to be available at each machine and clearly marked, visible and easily accessible.
- No safety device of any type should be by-passed or otherwise be prevented from carrying out its intended function.
- Exhibitors are responsible for ensuring that machine operators and those involved in any demonstrations are suitably trained and qualified. They should also be provided with adequate protective equipment and work wear.
- Visitors to the exhibition are not permitted to operate machinery or take part in demonstrations.
- All sources of power to and from the machines including electrical, hydraulic and pneumatic should be provided with a local isolator which should be switched off when the machine is not being demonstrated.
- A clear, approved Perspex or polycarbonate screen of a suitable height to act as a barrier should be positioned between the demonstrator and the visitor when carrying out demonstrations with any nailing or stapling tool. Users of such tools should also wear suitable protective equipment.
- Where electrical power is to be connected to machines or other equipment the Exhibitor are to submit to the Organisers (via Johanna - standapproval@montgomerygroup.com) and the Electrical Contractor (Fully Connected NEC) a plan of their stands indicating the location and power requirement in each case. Exhibitors have a duty to ensure that machines, apparatus and equipment incorporating pre-wired units comply with the venue regulations before they are installed on the stand.
- Portable electrical equipment shall be used with the minimum of trailing leads and NOT be left unattended. No electrical cables are allowed to cross gangways, passageways or emergency exits.
- Machinery is required to include adequate dust and waste extraction systems to meet safety and environmental regulations.
- Dust extraction systems need to incorporate ATEX compliant dust explosion relief panels directed vertically towards the roof space. Where the design of the extraction system is such that the explosion relief panels cannot be sited so as to discharge vertically the explosion relief panels are to be sited at least four metres above the floor level. Further HSE guidance on the fire and explosion hazards of wood dust can be downloaded free of charge from www.hse.gov.uk/pubns/wis32.pdf.
- To minimise the deposition of dust a minimum conveying velocity of 20m/s should be ensured. Fans are to be kept running for a brief period after machines have been switched off in order to clear the ductwork.
- Flexible ducting of all types are required to be earthed.
- Dust hoppers and bags need to be emptied each evening and waste removed from the hall without delay. The organisers have arranged for a production waste skip only in the loading bay for all exhibitors to use. This skip will be monitored to ensure only production waste is put into the skip. At the end of the show all waste needs to be removed from the hall please see Cleaning under the General Information Section if you require details for hiring bins or skips.
- Timber used for demonstration purposes are to be checked for metal foreign objects to eliminate the risk of sparks.
- Where ducting crosses gangways it has to be no less than 3.5 metres above the hall floor. It may not carry signage or promotional material of any kind. All dust and waste extraction systems over 4m in height are required to be set back 0.5m from the open perimeter of the site.
- Local Exhaust Ventilation (LEV) systems and airflow: Whilst there is not a specific legal requirement to fit air-flow indicators you are required by law to ensure that your LEV system is suitably maintained. A simple means of checking that the flowrate is maintained is the use of air–flow indicators at the hood. An air-flow indicator is currently the only method that will show the operator immediately when a problem occurs. (HSE’s LEV Guidance HSG 258(1) recommends that these are fitted). As an LEV Exhibitor you need to ensure that visitors are advised of all of the options available with your product.
- Single Bag Extraction Units/Unenclosed Sock Collectors – PLEASE NOTE: As detailed within the HSE Information Sheet No.32 “These would quickly disintegrate if the contents were ignited but would not produce high explosion pressures or widespread effects. Fire risks may exist, so if unenclosed, ensure the following is applied.
- DO NOT POSITION THEM WITHIN 3M OF OPERATIVES/VISITORS, COMBUSTIBLE MATERIALS OR WALKWAYS
- OR PROVIDE A SUITABLE BAFFLE OR DEFLECTOR PLATE OR ENCLOSURE.
- Under no circumstances may Machine Tables, including moveable / sliding tables when demonstrating machines are allowed to project over the stand space taken by the Exhibitor. In such cases, tables are to be locked in position to prevent this taking place during demonstrations.
- The use of Air Lines for the blowing down of exhibitor’s machinery during the event open period (including airlines that are fitted to machinery) is strictly prohibited by the HSE.
- Exhibitors and their Contractors should ensure that they are aware of the location of the first aid facilities whilst working onsite.
- CNC Routers/Machining Centre – exhibitors are required to ensure that machines are guarded to prevent access to all dangerous areas of the machine. To protect exhibitors and visitors, extra guarding maybe required to prevent accidental contact with cutting areas, tool changers, which could include perimeter fencing/ barriers. CNC Machines are currently a concern with the HSE so please contact the organisers should you be wishing to use one.
- Noise – exhibitors have a responsibility to ensure noise levels are kept as low as possible during all periods of the exhibition. Exhibitors are asked to consider all aspects of their machinery/equipment to ensure there is not unreasonable noise produced, taking into account staff, neighbouring exhibitor and visitors. For additional information, please see HSE WIS 13.
The HSE will be visiting the exhibition. Please see on the following page HSE GUIDANCE ON THE EXHIBITION OF MACHINERY. For further information contact Michal@i-l-s.co.uk
HSE GUIDANCE ON THE EXHIBITION OF MACHINERY
What should you know and do…?
Many European product supply Directives, including the Machinery and ATEX Directives, and the UK law implementing them such as regulation 3(2)(b) of the Supply of Machinery (Safety) Regulations 2008 permit in restricted circumstances the exhibiting of non-compliant products.
This is provided adequate measures have been taken to ensure that it does not harm any person at the event including those demonstrating the product. Also required is a suitable notice displayed with the product saying that the product will be brought into compliance prior to any supply. The notice needs to comply with the requirements of the relevant Directive and UK regulations.
Machinery which is not being operated will not usually present many hazards at exhibitions, although suitable safety measures should still be taken (e.g., to ensure stability, prevent falls from any access, contact with sharp edges, etc.).
Where the product is being demonstrated the requirements of PUWER, LOLER and other use legislation (e.g., Electricity at Work Regulations, COSHH, etc.) are required to be met, for example: by guarding dangerous parts, checking any lifting equipment is safely installed, making safe and secure electrical connections, preventing harm from hazardous fumes, etc.
The necessary measures for safety and health during trade fairs, exhibitions and demonstrations should be determined by undertaking a suitable and sufficient risk assessment. This needs to take into account the exhibition / demonstration environment, including any health and safety rules which the host organisation may impose, and the people (including in some cases children) that will be present, who may be unfamiliar with the hazards presented by the equipment on display.
Action from Exhibitors…
In relation to LEV systems, you are to ensure compliance by physical means and risk assessment. You have a duty of care to ensure all persons are protected in the event of explosion / fire.
Further HSE guidance on the fire and explosion hazards of wood dust is contained in the HSE Wood Information Sheet (WIS 32) which can be downloaded free of charge from this HSE link - www.hse.gov.uk/pubns/wis32.pdf.
HSE are always present at the exhibition and are always looking for compliance. LEV/Dust control will have a bigger agenda this year as HSE have been concentrating on this area with pro-active inspections in the sector and it is likely this will continue. Since the 17th of January 2020, the Working Exposure Level for wood dust (Hardwood and Mixed Dust) has been reduced from 5mg to 3mg per m3. Therefore, exhibitors are required to ensure this new level is met.
Risk Assessment
Exhibitors are required to complete a detailed risk assessment. A copy must also be available on the stand for presentation should it be requested by the venue, the HSE or the Local Authority. If it is considered that unsafe practices are being undertaken, they have the authority to close down the stand.
Risk Assessments do not just relate to the building of the stands. It also needs to cover the activities of ALL exhibitor's staff while they are onsite, whether this is lifting boxes during Build-up or a Demo during the Open Days. The Risk Assessment must be suitable and sufficient and needs to identify all significant risks to your own staff, other exhibitors, visitors etc. that may arise from your activities.
Significant risks are those which are reasonably foreseeable in terms of probability and severe enough in outcome to warrant consideration, i.e., they are more than trivial.
The Risk Assessment is the most effective way of documenting, assessing, and controlling risks and under Health & Safety legislation is an absolute legal requirement.
Completing a Risk Assessment does not mean that you are guaranteeing that there will not be any accidents on your stand. It means you have simply taken the time to think through your actions in advance and on an on-going basis. By filling out a Risk Assessment you will be able to reduce the risks of an accident happening or the severity of the accident if it does. If you were unfortunate enough to have an accident on the stand, you may need to prove that you took all reasonable steps to prevent it happening; a risk assessment would be part of this proof. Without it you could be found liable (both personally and corporately).
Click here to find the risk assessment template or for further assistance contact your own company’s Health & Safety Officer or visit the HSE website.
We are happy to provide help and advice on completing a Risk Assessment please contact Sophie Wood.
Stand Building Risk Assessments
These must not be confused with the Exhibitor Risk Assessment and relate solely to the building of the stands, whether they are a Space Only, a Shell Scheme or an Organiser Build Package. As an exhibitor if you appoint a contractor to build your stand, they will complete the Stand Building Risk Assessment as part of the CDM Regulations. If you are building the stand yourself, you will need to complete the Stand Building Risk Assessment as part of the CDM Regulations. Shell Scheme Stands and Organiser Build Packages are the responsibility of the contractors appointed by the Organisers. This is to be submitted in the Space Only Plan Submission Form.
Working at Height
Anyone who will need to work at height when building or decorating a stand at the show (this includes any form of step or ladder) should understand and follow the Working at Height Regulations 2005 (as Amended 2007). Falls from height are one of the biggest causes of workplace fatalities and major injuries.
Before working at height, you must work through these simple steps:
- Avoid working at height wherever possible.
- Use work equipment or other measures to prevent falls where this cannot be avoided.
- If working at height cannot be avoided, use work equipment or other measures to minimise the distance and consequences of a fall should one occur.
Figure 1 below gives further guidance for each of the above steps to help you comply with the law and can be found at http://www.hse.gov.uk/pubns/indg401.pdf
You should ensure:
- as much work as possible is done from the ground.
- workers can get safely to and from where they work at height.
- equipment is suitable, stable and strong enough for the job, maintained and checked regularly.
- workers do not overload or overreach when working at height.
- workers take precautions when working on or near fragile surfaces.
- protection is provided from falling objects.
- you know the procedure should any accidents occur – see Emergency Precautions and Procedures.
The Association of Exhibition Organisers (AEO) have developed an online information resource for use in relation to safe working at height. Please visit www.stop-the-drop.co.uk.
The Working at Height 2005 Regulations can be viewed at: The Work at Height Regulations 2005 .
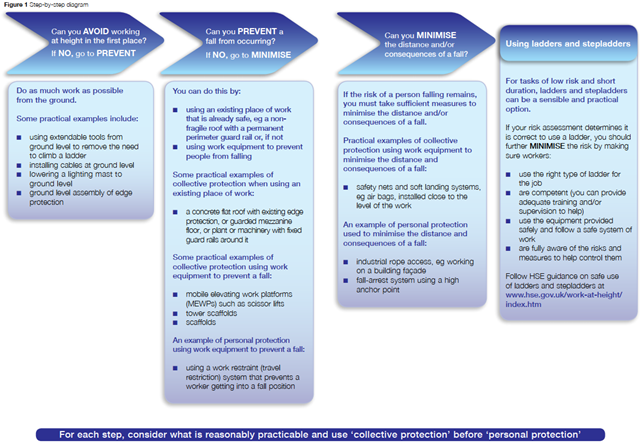